Got a question? Something on your mind? Find the answers here.
1. What is Ozone: Ozone (O³) is a powerful oxidant. Its actions can kill living cells upon contact. It can damage tissues of the respiratory tract causing inflammation and irritation which can result in coughing, chest tightness, shortness of breath and worsening of asthma symptoms.
2. Ozone Problem Indoors: Equipment such as photocopiers, laser printers and certain air purifiers can emit ozone indoors. Air purifiers that purposely emit ozone, called ozone generators, should not be used in occupied spaces as they can emit unsafe levels of ozone.
3. Air Cleaning Devices are regulated in California: Air Cleaning devices sold in California – including over the internet – must meet CARB regulation requirements.
4. The Ozone Limit for the CARB Program is 0.050 ppm*
* PPM = parts per million.
5. CARB Air Cleaner Certification Process: There are multiple steps to getting an air cleaner certified by CARB plus a labeling requirement for device being marketed and sold.
- Submit Application Number request form to CARB.
- Download and complete the CARB application. Put application number in right upper corner of the form.
- CARB can assist you in knowing which models need to be tested.
- Contact Blue Heaven Technologies for Ozone Testing of in-duct air cleaners.
- Blue Heaven only needs one unit of each type for testing. Each unit shall receive the appropriate number of tests per the standard.
- CARB requires chain of custody procedure on items being tested. Blue Heaven has procedure in place for this.
- CARB requires all Blue Heaven Technologies in-duct testing to be accompanied by a cover letter from Intertek Testing Services NA.
- Blue Heaven Technologies and Intertek Testing Services NA work together to ensure a smooth application process w/ CARB.
- Once the device is certified, CARB’s labeling requirements must be implemented.
Typical Dust Concentrations
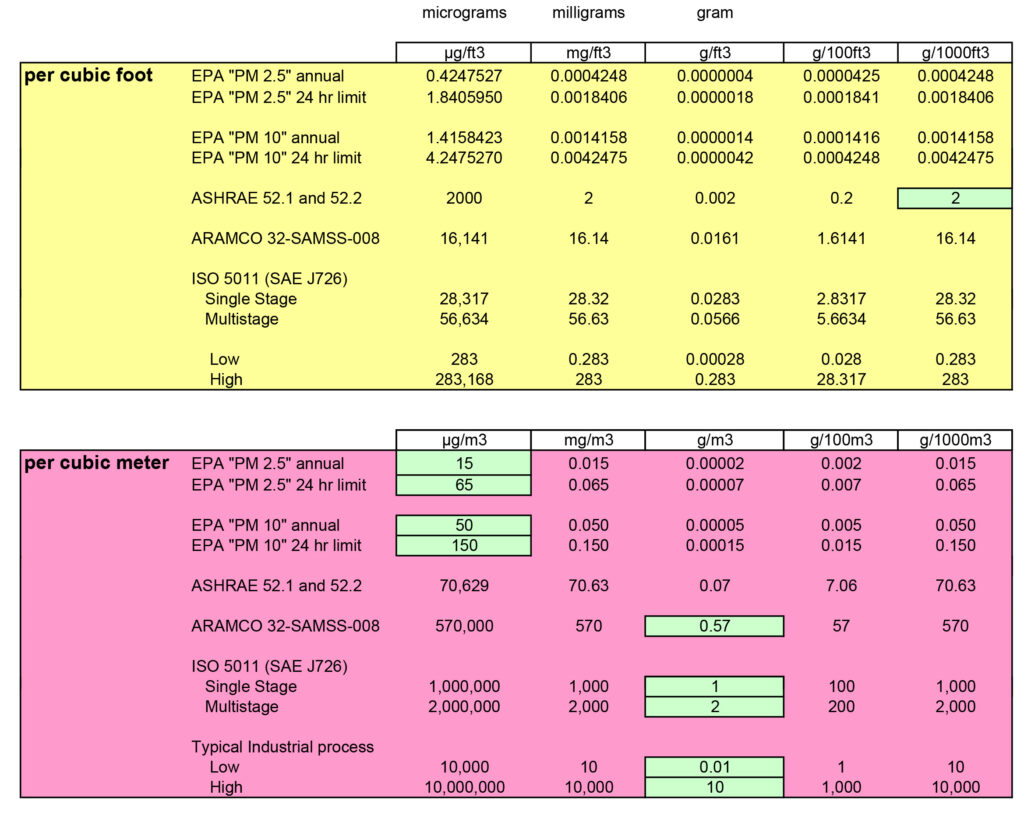
Yes it can. But like most technical questions, there are some rules and conventions that need to be understood in order to make dependable filtration decisions using ASHRAE 52.2 data.
Terminology is Important!
ASHRAE 52.2 testing generates two different performance numbers with two different names. This is because the filters test results can be used for more than one application or use. The two names are:
1. “Efficiency” – where the performance is measured in terms of total numbers of particles in the air upstream and downstream of the filter.
2. “Arrestance” – where the performance is measured in terms of total mass of particles in the air upstream and downstream of the filter.
“Efficiency” is used to make decisions about critical applications where the impact of very small particles that pass through the filters can be important – examples would be hospitals, health care facilities and some heating and air-conditioning applications. “Arrestance” is used to make decisions about industrial processes and manufacturing applications where the total amount of dust that passes through the filter can be important – examples would be manufacturing plants, processing plants, power generation equipment and other heating and air-conditioning applications.
The point – this customer is clearly interested in an industrial application because they have asked for performance using mass/weight terminology – grains per cubic foot in this case! By the way – There are 7000 grains in one pound! It’s a really long story!
But the units are important too!
The units to measure arrestance percentages in an ASHRAE test are typically expressed as a concentration of grams per 1000 ft3 of air. But since the total amount of airflow coming into and out of the filter remains the same during a test, you can drop the amount of air in the calculation and simply call it “grams” upstream and downstream of the filter. But you could also choose to use any concentration units you wanted to. Since arrestance is expressed as an efficiency percentage, you could use grams per cubic foot or pounds per cubic yard or – in this case, grains per cubic foot. No matter what units you pick, the measured arrestance percentage remains the same. Which brings us to the real point. It has been empirically shown many times that the measured arrestance of a filter in an ASHRAE test gets better as you go up in MERV ratings. The arrestance actually becomes too good to effectively measure above MERV 14. The filter in question here had a MERV rating of 12. If you reference the table below – Table E-1 Application Guideline from page 45 of the 2012 publication of ASHRAE 52.2 standard, you can see that the arrestance for a MERV 12 filter is a minimum of 95%. Since we have established that:
1. the units used do not impact the arrestance number percentage and
2. the arrestance for a MERV 12 style filter is above 95%
We can propose that the arrestance of the filter in question is defendable as greater than 95% removal of “grains per cubic foot”.
This is a question we get frequently. And it’s the one most all of us were asking when we first started getting data during the development phase of the standard. Since then, the phenomenon has been well studied, understood and explained.
SHORT ANSWER: The two-word answer is: “Particle Bounce”.
HOW DOES AN AIR FILTER WORK: An air filter is a random arrangement of fibers. Particles are caught on the fiber surface (not trapped in the holes like a sieve). If a particle moving in an airstream collides with a fiber, it sticks to it (is captured by the filter). All other things being equal, the bigger the particle, the higher the odds it will hit a fiber. These “higher odds” translate to the words “higher efficiency” in filter terminology.
Restated – the bigger the particle, the higher the efficiency. The curve of efficiency vs particle size should never drop off. But it does. Why? That was the question, of course.
LONG ANSWER: The answer may be more obvious to a non-filter person than it was to some of us who consider ourselves “experts.” Have you already asked “Why does a particle stick when it hits a fiber.” Well, it was an assumption to simplify the calculations and it seemed justified by what we knew at the time. But like a lot of things, if we use logic and take the example to extremes, that is, to absurd limits, it may shed some light on the subject. In this case, the absurd example is a baseball bat, which is a “fiber”, and a baseball, which is a “particle.” No one ever expects this “particle” to stick to this “fiber” when the batter swings. So the assumption is false with really large particles (73,660 μm in this example) and really large “fibers”. Take my word on the next statement – “With small particles (say 0.3 μm), the assumption of sticking is true”. With these two extreme examples, logic says there is a particle size somewhere between 0.3 and 74,000 microns where the particle bounce phenomenon starts. And maybe when it starts, it doesn’t transition immediately from 100% sticking to 100% bouncing. In other words, there is a range of particle sizes where some particles will bounce and some will stick.
It might bounce once and then stick on a second collision (with a different fiber), or bounce twice and then stick on the third collision etc. But the efficiency drop occurs when the particle bounces multiples times from fiber to fiber as it ricochets through the filter media, coming out, (still airborne) on the downstream side without being captured by the filter.
CONCLUSION: Tests like ASHRAE 52.2 show that the transition from sticking to bouncing occurs in the 3-10 μm range of particle diameter. The drop in efficiency as particle size gets bigger is real and is due to “Particle Bounce”.
ONE LAST POINT: When it occurs, “Particle Bounce” generally happens in filters that are MERV 8 and below. The lower the MERV the larger the fibers, as a rule of thumb. This bounce phenomenon requires a combination of large particles (where we can be quantitative) and large fibers (where we can only be qualitative in this presentation).
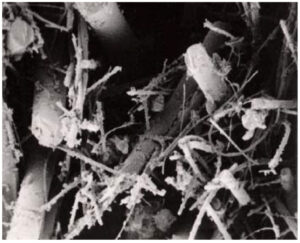
Photograph from electron microscope at 1000X magnification. Partial cross section of dirty air filter media (MERV 14). The airflow direction was from left to right. The fibers are glass with smooth circular cross section. The large fibers are 5 μm diameter; the smallest are less than 1 μm. The collected dirt particles are evident on the fibers wherever the “smooth” fiber surface looks “bumpy” or “fuzzy”. Most of the collected particles here are smaller than 1 μm.